To make sure your designs look perfect right up to the edge of the page, we print on larger sheets and then trim them down. This helps us avoid any unwanted white borders caused by tiny shifts during printing. Here’s a simple guide:
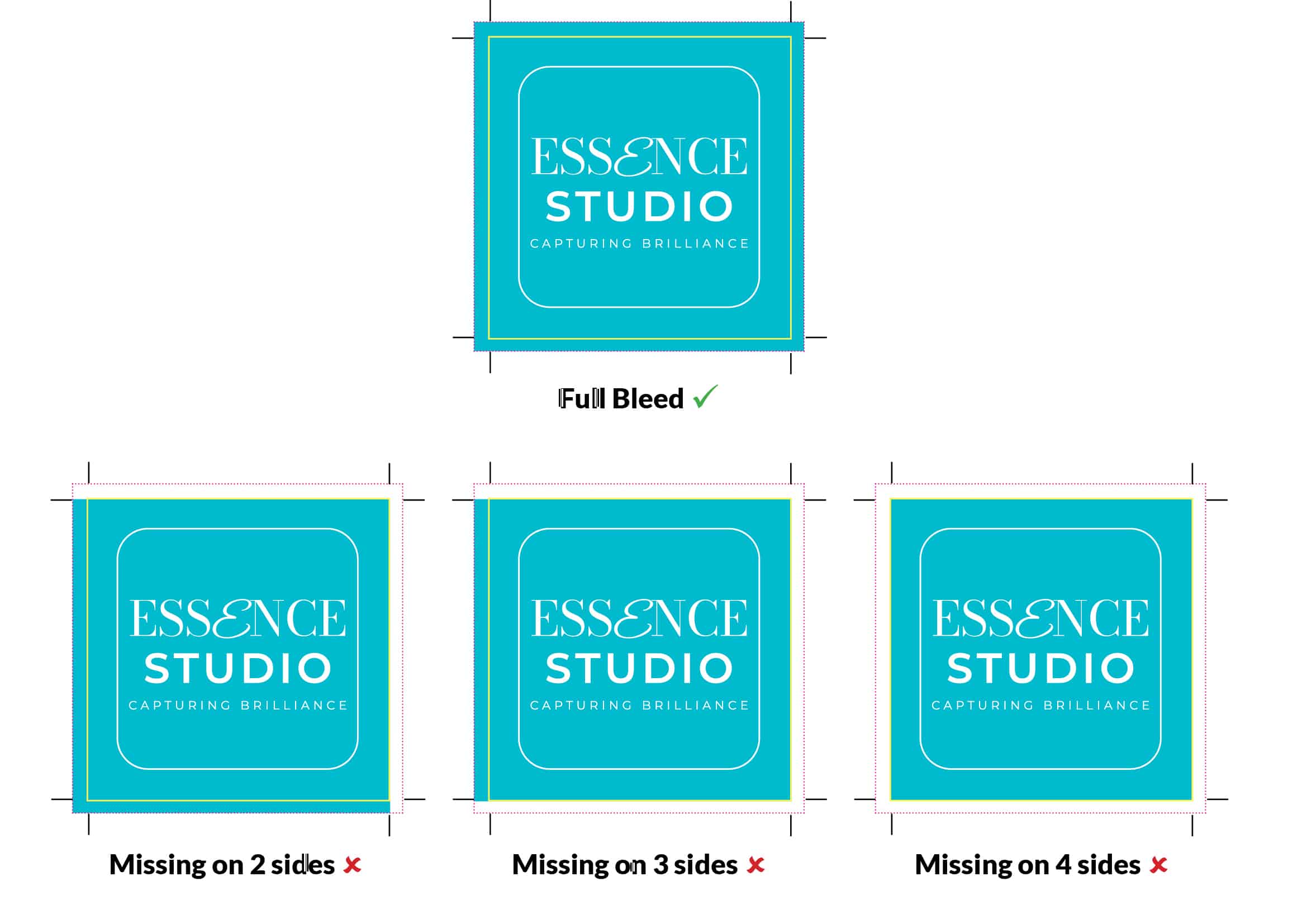
– Why it’s Important: This extra space ensures that even if the paper moves a little while being cut, your design still goes all the way to the edge.
– Example: For a business card that’s 85mm x 55mm, your design should be 91mm x 61mm. This way, we cut off the extra 3mm on each side, leaving a perfect 85mm x 55mm card.
2. Crop (or Trim) Marks: Cutting Guides
– Why they’re Important: These marks guide us to cut your design to the exact size, ensuring everything looks neat and professional.
– Placement: Trim marks are placed 3mm away from your design’s edge, so they don’t show up on your final print.
Need Help?
If you’re unsure about setting up your artwork with bleed and trim marks, we’re here to help! We can add these for you for a small fee or guide you through the process. Read more on our Artwork Fix Service page.